Wood Strength 101
My 18″ bowsaw broke last night. It was a newly made one I bought from CME Handworks a few years ago and the saw works great. The arm breaking should not be a reflection of the maker other than his choice to use Maple. I believe that over the last few years, I have weakened the arm until last night it just gave up. I have not been over tensioning it nor do I leave it under tension when not in use. In other words, it just wore out. This should be expected since the wood choice was not the best to begin with. I posted this on Keek and within minutes had shocked comments on all my social platforms that Maple isn’t the best choice. So I thought a little wood 101 was in order. I’m going to purposely over simplify a little here, so you wood nerds can feel free to beat me with your lumber rulers and moisture meters in the comments below.
Hardness Does Not Always Equal Strength
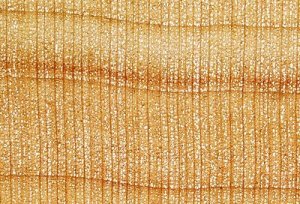
The tiny pores are spread all over so there is no distinct plane of strength and little room to bend.
A few of the above mentioned comments stated with dismay that Maple is so strong and what should a bowsaw be made from? Yes Maple is very hard, but hardness should not be confused with strength. Usually the harder a wood, the more brittle it becomes. The hardness is a reflection of the wood’s density. The tighter packed the fibers, the less space in between them and less compression. This means that the wood doesn’t bend much and very often you will find a higher MOE (modulus of elasticity) rating accompanies the species. When something doesn’t flex under a dynamic load, it relies only on the fibers to withstand the force and often will break or micro cracks will develop. When this break occurs it usually shatters instead of splinters. A good example of this is a Maple baseball bat versus an older Ash bat. In this case, Maple is a diffuse porous wood so it is very tightly packed and the open space (the pores) are tiny and evenly spaced in no particular pattern throughout the wood.
The Ash is ring porous with larger pores that are ordered in neat rings thus leaving non porous material also lined up in between the pores. This makes for long strands of fibers that have room to flex into the open pores in a predictable manner. Here is a food analogy you can use to illustrate this. Grab some spaghetti and hold 10 or 12 pieces loosely in your hand. Now bend them. They will flex a bit with the open space around them. Take those same pieces and grip them tightly so they are packed tightly together. Now bend them. They will snap very easily because there is no room to flex into. This is the same material with the same hardness properties. So hardness alone can’t be used to determine the strength of a wood since both Ash and Maple have similar Janka hardness ratings. It is a good starting point however especially when you get into hardness ratings above 1500.
Kiln Drying Makes the Cookie Crumble
Now add to the mix a kiln dried wood. Kiln drying hardens the wood fibers just like most things harden when they are baked. Take a flour tortilla and put it in the oven. In a few minutes you have a crispy tortilla that will break when you try to bend it. This is what is happening in a lumber kiln to some extent. Kilns also use steam to lower this shock and keep the fibers more pliable. Take that same tortilla but wrap it in a wet paper towel then bake it. You will get a warm, but more flexible tortilla. Anybody getting hungry yet? Air dried wood does not rely on heat to force evaporation so the fibers do not harden and retain their natural pliability. The woods that are the most strong and handle dynamic forces best are ones that are air dried regardless of species.
Sawing Goes Against the Grain
Sawing by its very nature cuts the wood fibers and rarely follows the natural grain. When you cut across the wood fibers you weaken the wood dramatically. Riving the wood splits it along the grain and exploits the natural weakness between the fibers while leaving long, continuous strands of wood fiber which are ridiculously strong. A board comprised of a bunch of short fibers relies entirely on the “glue” between the fibers to whole it together. Cut a 1 inch piece off a board and you will see how easy it is to break in half across the grain with just your fingers. The “glue” isn’t strong enough to withstand even a little force. Sorry no food analogy here, if you can think of one let me know.
What is Strong?
In all of the cases above I am thinking about a situation where dynamic stresses will be placed on the wood. Let’s face it, if we make furniture this is most of the time. From sliding a table across the floor to the extreme of leaning back in a chair, our joinery and the wood itself is being subjected to varying levels of force. A bowsaw is an extreme example where a rigid cross piece aligns it’s strongest dimension against the weakest dimension of the arms. Then tension is applied by shortening the distance between the arms at the top while restraining the bottom with a saw blade. This is akin to breaking a board over your knee. It doesn’t take much force to break it. The bowsaw arms are the same and you can easily snap one by applying too much tension. Likewise the constant tightening and loosening will wear out the fibers. Take a credit card and bend it and straighten it repeatedly. It will become very weak and eventually break.
So how does this help us choose a strong wood? It is all situational and one needs to recognize where the force will be place on the wood and how much. A keepsake box sees very low stress so there is nothing to worry about. A dining chair sees a lot of stress and a combination of well planned joinery and wood selection is in order. Usually chair makers rely on riven wood and optimize their joinery to place the strong dimensions so they are resisting or supporting each other. Strength requirements vary dramatically and in most furniture it isn’t something we need to worry about. It’s when we get into the stuff that takes the most dynamic pressure that we need to start planning. Axe handles, chairs, roof trusses, and bow saws.
In a perfect world we could all be working with riven and air dried material. It would be ring porous to allow for a natural bending tendency. When some of these factors can’t be found then the others become all the more important. The hardest is probably the air dried thing. Most of us only have access to kiln dried material so we need to choose our species wisely and if possible split out our parts to maximize the long grain. If you don’t have the extra stock to split it out then all you have going for you is choosing the species wisely and a nice ring porous wood is your best option. Think Ash, Hickory, Oak, or even Walnut (semi-ring porous).
So with all of this in mind, why did I make my own turning saw out of Maple? Simple answer, because it was pretty and I had it on hand. This saw needs much less tension with a shorter and narrower blade so it will perform nicely and has for some time. However I won’t be shocked when one day it snaps on me as I’m probably introducing micro fractures every time I use it. The model available from Gramercy however uses Hickory and will outlast my shop made one easily because it is a naturally bendy, ring porous wood. My larger bowsaw was expected to tension a much wider and longer blade plus cut through thicker stock. It makes sense then that the more heavy duty the tool, the more thought needs to go into wood choice.
If I can leave you with anything it is not to run for the hills panicking that all your projects will fall apart because you are using a hard and brittle wood that is kiln dried and sawn. Heck even my kiln dried, sawn, Maple bowsaw lasted 4 years of hard use before giving up. The key is that when it snapped I was not surprise at all and even expected it. When I remake the arm, I will make two and use a more appropriate wood species. The bowsaw is an extreme with the forces it is expected to withstand, but hopefully a look at these principles will help you understand the material we all love that much more.
Now go make a spaghetti burrito.