<Workbench style=”aligncenter” />
I’ve been living with my workbench smack in the middle of my shop for many years now. Shortly after I built it, I placed it up against the back wall under a window and I think it lasted a week there before I moved it to the center of the room. A good workbench will disappear in use because it does everything you need it to do without even thinking about it. I think of the key components to this magic disappearing act is placing the bench in the center of the room.
It has 4 Sides, Use Them
I am constantly setting up specific work zones on my bench. In fact I even designed a few of my shooting boards to work from the end of the bench rather than the longer side. Often when I’m in the middle of the joinery phase of a project I’ll have a shooting board set up to true and size parts, a bench hook for sawing parts to size, a paring hook for refining joinery, sometimes my miter box is nearby for quickly setting specific angles, and finally there is space set aside by the leg vise, sliding leg vise (I usually mount this on the opposite side from my leg vise too), and the end vise where I may be doing another operation. These are a lot of work zones that would require moving stuff around unnecessarily if you have your workbench pushed up against a wall. With a lot of workbenches hitting 24″ wide and greater you have a lot of wasted space if you can’t access a side blocked by a wall.
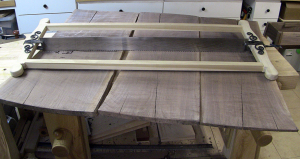
When I’m resawing with my 48″ monster, I have to stand off the end of my bench for proper alignment.
Milling Sometimes Requires Switch Hitting
In a perfect world all our boards would have grain that runs in one direction…but rarely does this happen. Especially on wider boards and always on figured boards, I find myself having to change directions and plane right handed instead of left. While I’m much better at it than I used to be sometimes my right handed technique just isn’t working so I switch to the other side of the bench and continue to plane left handed going the other direction. And when I’m working a really wide board over 16″ it is much less tiring to work on the other side of the bench rather than reaching all the way across the top from the same side.
Finish in the Round
I don’t have a dedicated finished table or space. All my finishes go on when the project is on the workbench. Being able to have 360 degree access if imperative. I tried a lazy Susan contraption once but it only worked well for smaller things so I went back to setting the piece up on Painter’s Pyramids and walking all the way around it. I have also discovered that just moving around the project also changes how the light hits the project and I uncover missed spots or areas that need more attention for one reason or another. This same principle works early on in my project when I’m choosing which boards to use for which piece of a project. Just changing my perspective helps me see the grain of a board better without flipping heavy boards around.
Truly this is the tip of the iceberg when it comes to the benefits of a workbench with 360 degree access. The fact is that like I said at the beginning of this, when the tool functions well, it disappears. There are probably benefits I haven’t even thought of because I unconsciously crossed to the end or opposite side of my bench to do something. To paraphrase Ferris,
“If you have the means, I highly recommend [placing your workbench in the center of the shop]”