My Joinery Bench at WIA
From the very first day I started the Hand Tool School, I have gotten requests about building a bench. It seems that despite my epically long Roubo build on this blog and gigabytes worth of data all over the net that we still cannot get enough of bench building. So, I admit it, I’m caving and building another bench.
I have fought this mainly because it can be a time consuming project, it takes up a lot of space, and frankly I’m in the mood to build furniture lately. So I’m compromising by building something that I could really use while incorporating many of the same techniques I would use if I built a Roubo, Continental, or Holtzappfel style bench.
Enter the joinery bench. Tim Williams first popularized this little beauty in early 2010. I haven’t seen much talk about it since (I admit I haven’t really looked either)but it is an idea that has stuck with me. I’m 6’4″ tall and I find myself stooping a lot when dovetailing and tenoning. The 9 drawers (built twice, don’t ask) on my tool cabinet had me hobbling around for a week. I love my Roubo, it is the best thing I ever did for my shop but the time has come for the joinery bench.
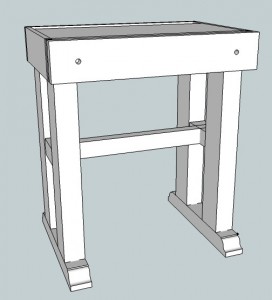
A general idea of my design so far.
I am going to begin building one in the next week and I will be showcasing the build in detail as part of semester 3 of the Hand Tool School. If you are not a member don’t worry, I will show some tidbits here and there on this blog, but more importantly, it will be my demonstration bench at the Hand Tool School booth at WIA in 2 months. Please stop by and help me break it in.
The preliminary design is basically a very short Roubo bench combined with a traditional trestle, Continental style. The main work holding device is a full width twin screw vise made from Benchcrafted’s new Moxon hardware. Beyond that, I have some details to hammer out still.
So where to start? The amount of ink spilled on the topic of which wood to use could fill many Olympic swimming pools and it is something to consider. Usually, I land on the side of whatever is most available in your immediate area.
Weight is a factor since this bench will be smaller in size. I don’t want to have it moving around on me. At the same time, I won’t be doing any major planing on it so it doesn’t have to be as stable as my Roubo. I have often found myself wanting to move my bench outside in nice weather but my 400+ lb Roubo does play that. Finally, this bench will be made to knockdown so the species needs to be light enough that I won’t bust a gut moving the individual parts.
Hardness is a factor but the opposite way of most people’s thinking. I want my benchtop to be softer than most of the woods I use in furniture so that my bench won’t marr my workpiece. My Roubo is made from Ash. It is hard; it was hard to make. That is why you saw more powered routers at work than router planes during that build. Softwoods are a great solution as they are cheap and readily available.
I also like to buy big pieces. Laminating up thick legs and a top is no fun, so the fewer glue lines I have the better.
Stiffness measured in pounds per square inch is a major factor for the Roubo style bench that has no supporting apron. The top material much not flex between legs. This is not as important for a short joinery bench but still something to consider.
Douglas Fir comes to mind immediately as a prime species. It is harder than Poplar yet softer than Cherry. It is relatively light, but heavy enough that when all put together, the bench will be solid. Additionally, I think my four thick post legs will be more weighty and stable than the cross leg design of Tim’s bench. Douglas Fir also has a very high stiffness rating which is why it is so commonly used in structural framing for Timber framed homes. Finally, I can get thick posts from the lumber yard where I work. So I believe I will be making my legs and substructure from Douglas Fir.
Not the top…
Remember when I said, “whatever is readily available”? I’m going to go against all the logical species selection points above and give in to my wood addictive side. I recently salvaged some 12/4 Quartersawn African Mahogany (the good stuff from the Ivory Coast) from the back of the lumber yard. Khaya Mahogany is heavy, but it is quite hard. The grain is tough to plane as well. The stiffness is ok, but not great. So what am I thinking?
It was a small piece only 34″ long but it is 18″ wide. Once surface planed I should be able to get 2 1/2 ” in thickness. The piece is weathered and warped so I will have to remove a lot more wood to get it flat. My design calls for a top that is 15×32 so it seems like fate that this piece should come into my hand doesn’t it?
I started removing some of the schmutz and yard grime then tackled some small parts with a block plane to see what I was dealing with under all the weathering. Some beautiful ribbon figure immediately presented itself and this will be great to work with. This slab is the perfect example that not all African Mahogany is created equal. The bad reputation that species gets is mostly due to so many local species get conglomerated into one “brand”. Khaya ivorensis from Cote d’Ivoire is some of the best stuff out there with consistent density and color. It will pose some hand planing difficulties with all that interlocked grain, but I like a good challenge.
I can’t believe I’m going to build another bench, and that I’m this excited about it!
So what do you think?
- Would you save the Mahogany for a “furniture” project?
- Could you use a dedicated joinery bench?
- What is your lumber of choice for a workbench?