Pepper Mill Repair
I made mention of this problem on the latest episode of Wood Talk Online and have been thinking about it more and more. For Christmas 2011 I turned several small sea salt mills to give as gifts. Wouldn’t you know it, but the one I made for my mother-in-law must have shrunk so that the handle won’t turn any longer. I told her I would take a look and can probably ream out the hole a bit to allow the mechanism to rotate again.
Obviously the wood I used must have shrunk a bit. Drilling a hole through any stock will open up more end grain through which the wood will dump moisture. Then again the hole for the mechanism arm was precisely drilled to be a tight friction fit so even the slightest movement would cause it to pinch.
When I brought the salt mill back into my shop I noticed 2 hairline cracks along the body. They were so tiny that only the maker would notice since we are the only ones who look that closely at our work. This raised a few alarms and when I tried to remove the mechanism from the mill I found that the whole thing was wedged tightly in place as the entire body had shrunk around it until the unforgiving composite material inside caused the wooden body to crack.
The first thing I did was check the moisture level of the stock I had left over from this salt mill thinking that perhaps it was high to start with. As expected, the blank was at a happy 8% which is typical for my shop this time of year. I wasn’t really concerned about it when making the mill as the Marblewood stock I used had been sitting in my shop for close to 5 years. Moisture content in general is something I don’t pay too much attention to when turning small object like this as there is no joinery involved and the piece is free to move how it likes. Obviously this case was different since I have to friction fit two pieces of the grinder mechanism.
In hindsight, it seems perfectly obvious that the wood would shrink. Remember this is a sea salt mill. Salt is a desiccant and therefore leached even more moisture from the wood at an accelerated rate. I did my best to take a moisture reading on the irregular surface of the blank and while I’m not holding my breath on the accuracy, it looks to be around 5%. So here is the problem: how the heck does anybody make salt and pepper mills out of wood when the very material meant to go inside of them will cause rapid shrinkage and binding around the mechanism?
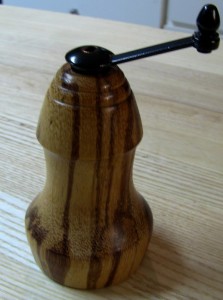
Patched, cleaned, and ready for assembly
Any turners out there with experience in this area? Are there better mechanisms that don’t rely upon a friction fit that I should be using? Do I need to pre-dry my blank under a light bulb or something?
Maybe the Marblewood is the problem because it is so hard and brittle. This is the first time I have ever used Marblewood so it is a bit of a wild card. I have not had any complaints from the others I gave this gift to and those other blanks are all made from Walnut and Maple.
Needless to say, I reamed the top hole then sealed the crack with thin CA glue, re-sanded, and applied a new coat of finish. I then dripped shellac down into the interior in an effort to somewhat seal the inside and possibly slow down the drying action of the salt.